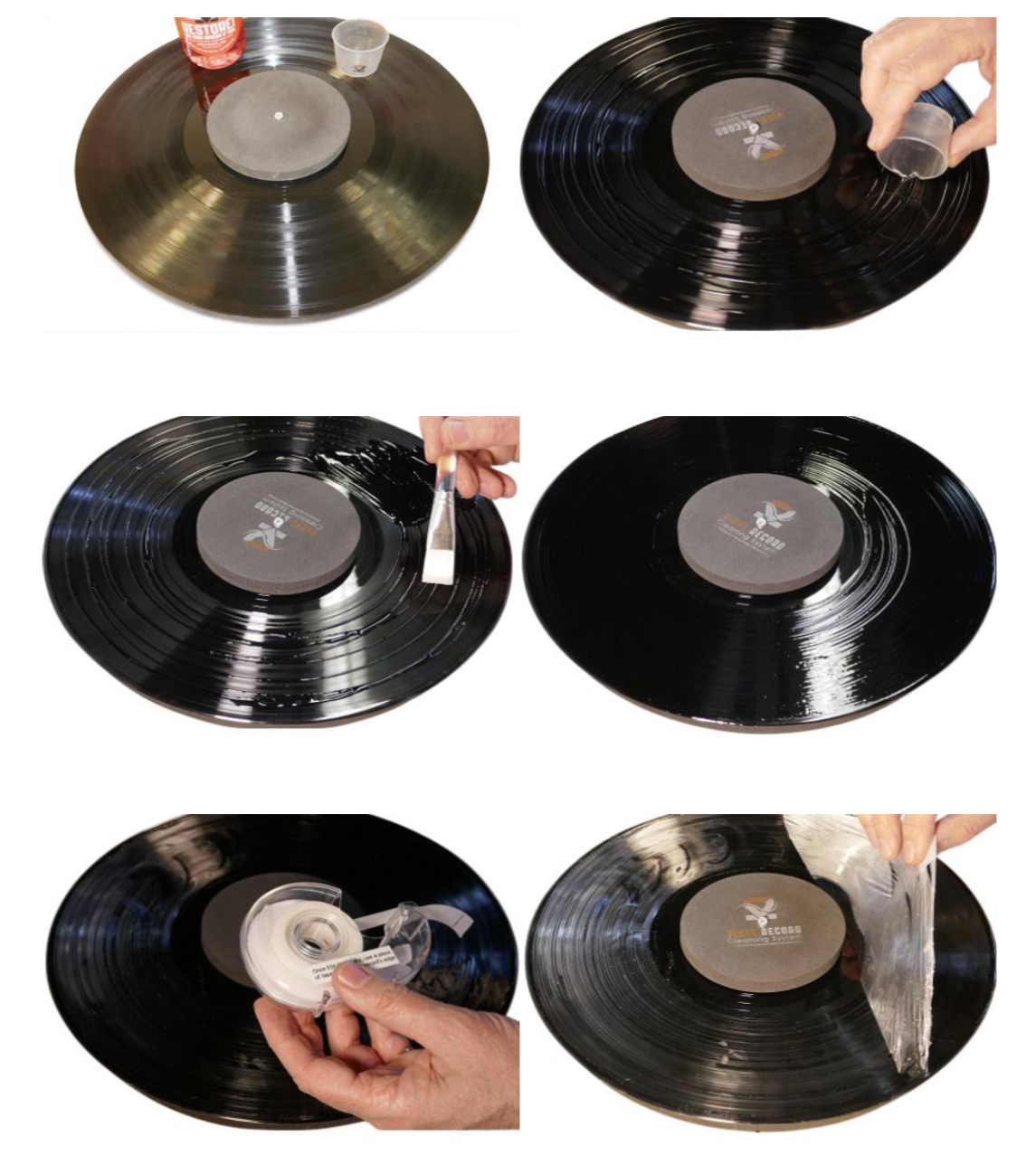
There are many things that go together well. Salt and pepper, sugar and spice, fish and chips, Kath and Kim, and dust and scratches on albums. Wait ... that's not right; dust and scratches on albums? They do go together, but that's the opposite of what we want. For as long as we have had analog audio reproduction, we also had the need to keep things clean. Even audio tape must be cleaned, and the trick is to avoid removing the actual bits of magnetic coating, or you will damage the tape. Turns out it's similar for vinyl records. You want to clean the dust out of album grooves along with other contaminants, ranging from tar and nicotine, liquor, beer, soft drinks, and even pizza grease. In short, albums don't get enough respect.
Since many vinyl lovers are bargain hunters, finding great albums at garage sales, thrift stores, and basements isn't all that uncommon and can be part of the enjoyment of collecting. The havoc that the oil shortage crisis of the ‘70s played with the stamping of vinyl biscuits into finished albums often brought with it a higher number of less-than-pristine pressings. So, cleaning is often more than just getting rid of dirt, it can also undo some of the manufacturing process artifacts.
In previous articles we've looked at different approaches to cleaning LPs, all of which used the same process: get the records wet, wash the dirt out, dry them, and voila - cleaned albums. We've also commented on a strange trend of using wood glue to clean albums, an interesting, but peril-fraught technique. Essentially, no matter the company, name, or machine that claims to clean your albums, most are just washing machines. Soak the grooves, then get the dirt and other stuff off the record, and then clean the dirt and water from the grooves, dry, and in theory, you end up with a perfectly clean album. But how reliable and effective is that process? Does it really remove all contaminants? Even the trend of new, and expensive ultrasonic record cleaners, are still washing the grooves, albeit with high frequency excitation to better penetrate and loosen dirt from the grooves, so, it's effectively a better washing machine. But, it's still a washing machine.
When our colleagues recommended that we take a look at a new process from Australia from The Vinyl Record Cleaning Company, our interest was piqued. It's not often that we refer to cleaning albums as fun. But, the unique Vinyl Record Cleaning System and VRC Restore! vinyl record cleaning film is a lot more fun than we expected. Cleaning records generally isn't a big thrill. Most vacuum-type machines are loud, wet, and a bit of a hassle. Some are quieter, or manual, or automated, but still a bit of a hassle. You just want to get to the finish line with clean vinyl and listen to music. It's a bit like doing the laundry, some people find it fun, I think we can agree that we all feel it's important, and some machines are less hassle then others. Interestingly enough, tests of the cleaning power of laundry machines, revealed how similar the results are, no matter how fancy the feature set is.
Remember, those tricksters who used blue markers on the edges of CDs? We figure they're the same folks who thought that coating albums with wood glue, letting it dry, then peeling it off was a sane thing to do. People swore about the improvement in sound quality, the ability to pull off dirt that wouldn't come off with washing. I'm all for off-label use, but wood glue was designed to glue wood together, not clean albums. It's also too viscous, and forget about the idea of testing the long-term archival impact on the vinyl. It is an intriguing idea, and while it might be fun for YouTube videos, it’s nothing anyone should bother with. And even a tiny bit of glue left in a groove might prove fatal to a stylus. So, while putting glue on an album might appear to be similar to the process used by the Vinyl Record Cleaning Company, that's as far as it goes. Don't confuse the two; VRC Restore! is designed for cleaning and restoring albums, and the other isn't.
Stephen Price is the inventor, creator, and audiophile behind the Vinyl Record Cleaning Company. Price went on to create an entirely different approach, using a peel-off mask, similar in principle to beauty mask products used by millions around the world to deep-clean facial pores. Price was kind enough to ship us a couple of their VRC System Kits, which provide everything you need to get started. It allows you to coat and clean several different sized vinyl records, complete with all the tools needed, and a nifty way to dry the treated records. The system is based around VRC Restore! solution.
Kit Contents:
Unlike most record cleaning techniques, such as the Record Cleaning Machine that we reviewed in the past, it's far more of a ritual to clean albums with the VRC system than with the simpler wash and dry method.
To get started, just place the album on the supplied VRC Platter turntable, and measure the recommended 5ml of the VRC Restore! into the supplied measuring cup, spreading it on the record surface. We found we needed a slightly heavier pour, and it was important to consider the humidity and air temperature, not so much for the pour, but for the drying time. Use the supplied brush to get a nice even coat. Seriously. It's fun and could be a good activity to get the kids to pitch in with you - it's like spin-art for albums!
Coat both sides of the record surface, then place the album with a spacer on the rack to dry. Should you do a batch of albums at one time? We were hesitant at first, simply because we wanted to complete the process for just one and see how it went. But after a few, you find a rhythm and realize you can easily do multiples in a session. You can't really screw it up. We found it challenging to try to peel the entire surface off all in one piece. But if your technique involves peeling multiple strips, the end product will still be the same.
As we began this review, our home was torn apart due to a kitchen project. We were worried about the construction and drywall dust polluting the process, so after a few months of delay, we unpacked our vintage Luxman PD-72 turntable and did some careful “before” listening, taking notes on pops, clicks, and audio quality, and that intangible sense of reproduction vs. reality.
The thing about the VRC is that it doesn't let you tweak the process much. True, when we started they offered four different formulas of Easy Spread n’ Peel, which have now been simplified to two formulas, one for 78 rpm discs, and VRC Restore! for normal LPs. The first few albums we did were a little difficult to peel. The film came off, but not evenly, and left lots of little bits to get off. And it was slow to pour, not as smooth and easy flowing as in their instructional videos. When I mentioned this to Price, he replied that the VRC solution wasn't meant to sit around for too long before use, so he was arranging to send me fresh solution. In the meantime, he suggested putting the bottle of VRC Restore! into the microwave for just 15 seconds. That tip made it work perfectly - it flowed smoothly and easily, and the pours and peels were much more even.
We made the mistake of letting the solution encroach on the label a few times, and it dutifully removed the bits of label where it touched, just as it removed dirt from the vinyl. Our advice is to pay careful attention to how you spread the solution and be sure to stop at the start of the exit lead-out groove. The puck that holds the album in place on the turntable also covers the label when you spread the solution, which helps to protect from accidental drips.
Does the VRC does work better than the more traditional washing systems? Is it on par with other comparable techniques? The short answer is yes. All the techniques cleaned albums, reducing cracks, pops, and scratches. All dramatically improved the sound, all worked well, however the VRC provided the least amount of resulting surface noise of the processes we tried in final listening.
It was clear to us that the VRC-treated albums were among the quietest in our tests. What really stood out was the lack of noise from the albums after use, with the combination of what we observed to be less static electricity, along with the normal clicks and pops, and diminished static crackle upon playback. One other benefit was a noticeable lack of static cling, therefore the completed albums didn't seem to attract as much dust as they previously had.
So, whatever Mr. Price was doing down under, it was working up here in the hinterlands of Philadelphia. In the meantime, we recommend that you order up a batch and take it for a test run. If you are going to clean your albums, choose a process and solution designed specifically for that task alone. Plus, it's fun!
In part two of this article, we'll get granular about how it works, theories of stylus and groove interaction, thoughts on the new and improved turntable, the simplified VRC solution choices, and the value of treating albums a second time. Part one of a two-part article.
Harris Fogel, Nancy Burlan, and Frank Schramm, Posted 4/7/2021
For more information on The Vinyl Record Cleaning Company visit: https://vinylrecordcleaningsystem.com.au